Blog
- Super User
- General Knowledge
- الزيارات: 3761
Why is the automatic lubrication system necessary in food processing areas?
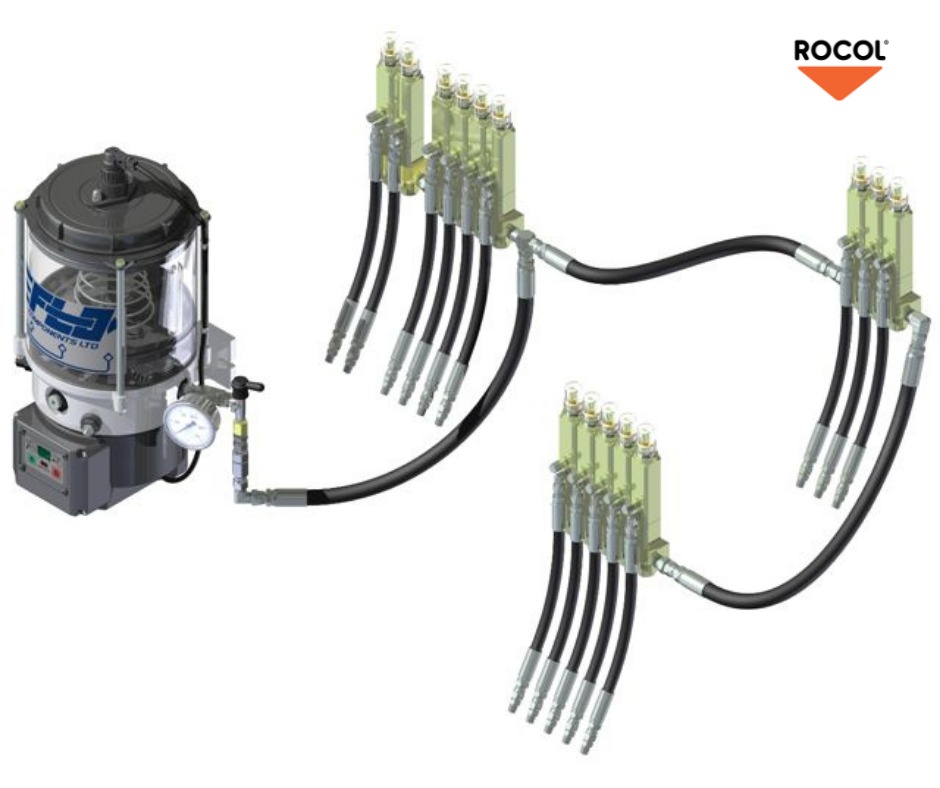
Productivity and extended uptime are key in today’s economy. Automatic lubrication systems have been designed to increase uptime of machines and vehicles. Next to that, automatic lubrication offers more advantages in terms of cost savings, durability, productivity and safety.
1- The Multi-point Challenge: Food and beverage manufacturing operations often have hundreds or even thousands of lubrication points in a single facility. Although automatic lubrication systems have been around for decades, much of this work is still conducted using manual labor, particularly when the lubricant is grease. While the food and beverage industry is moving toward higher-speed, higher-volume automated equipment, it is becoming increasingly impractical for the industry to depend on labor-intensive manual grease gun lubrication. ''Bearing giant SKF has estimated that 57 percent of all bearing failures are lubrication-related," explains Richard Hanley, president of Lubrication Scientifics. "That rate can be reduced dramatically by automating the lubrication process, which ensures that the right amount and type of lubrication are delivered to every equipment bearing point." Automated lubrication systems can be used in a wide variety of industries in addition to food processing, including the pulp and paper, chemical processing, steel, petrochemical and mining industries. From an economic point of view, the payback period for most of these systems is less than a year. In some cases, engineered lubrication systems with advanced monitoring capabilities can save millions of dollars in downtime costs per year. Automated lubrication systems eliminate the cost and sometimes hazardous task of manually applying controlled amounts of lubricant to multiple equipment locations at frequent time intervals while the equipment is operating. "More frequent delivery of smaller amounts of lubricant is particularly important to bearing points on high-speed equipment," Hanley says. "This prevents overheating the bearings due to excessive lubricant buildup and ensures longer operating life."
2- The harsh environments: Food-processing plants are exposed to some of the harshest environmental factors, including extreme room temperatures and mandatory caustic wash-down procedures. U.S. Food and Drug Administration regulations require all processing lines and equipment be adequately sanitized as often as necessary. In the food-processing industry, corrosion problems are normally prevented through the use of equipment made of stainless steel. However, since a broad offering of stainless-steel metering valves has not been readily available, the only effective anti-corrosion solution for automatic lubrication system components has been to enclose the plated-carbon-steel metering valves into stainless-steel enclosures.
3- System Types: automated lubrication systems can be beneficial for plants that need to supply precise lubricant amounts to many points, ensuring longer machine life, safe operation, reduced unscheduled downtime and more economical operating costs. Automatic lubrication systems come in many types, such as single-line parallel, series progressive, dual line and multi-line, each with its specific advantages and application areas. Because of this wide range, generally any application can be lubricated with an automatic lubrication system.