Blog
- Super User
- General Knowledge
- Hits: 2009
How to detect an early premature bearing failure
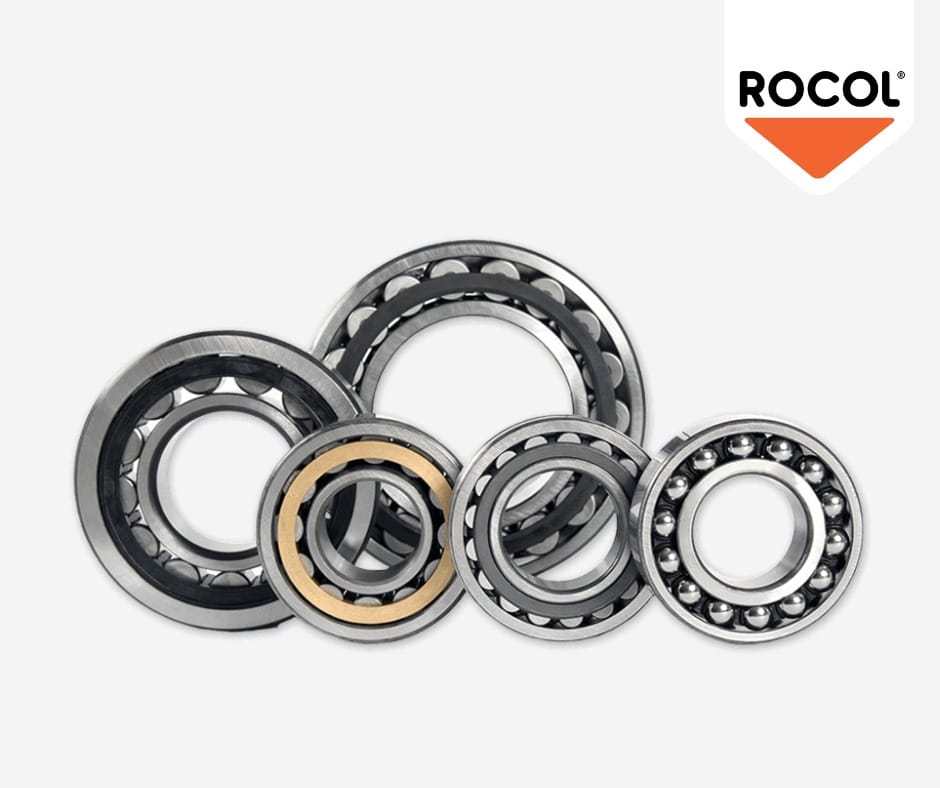
1- Monitoring Bearing Condition:
Machine bearings are generally monitored through vibration analysis, oil analysis and/or ultrasound techniques.
In most cases vibration analysis and oil analysis are still the best ways to determine bearing health. Unfortunately, it's not always possible or affordable to use these methods in hostile production environments where staff or technicians cannot easily access the machine without taking it offline, or cannot access the machine due to hazardous conditions or inconvenient locations, and that of course make vibration or oil analysis expensive at best, or even impossible.
There are many industries and production environments where bearing failure represents catastrophic loss. Photographic film and paper manufacturing, chemical processing and metalworking plants are a few examples of industries that depend greatly on bearings, but where bearing accessibility can be a major problem. Most manufacturers have at least some vital equipment in areas that are not easily accessible.
Wheel bearings on railroad cars are a specific case in point: they are underneath trains, which are not hospitable places for performing these tests while the cars are moving. Secondly, there is no practical method of checking all such wheel bearings in a timely manner because of the sheer number of them in use.
Currently in the railroad industry, the only practical method for detecting impending bearing failure is to use so-called hotbox detectors. These are infrared sensors located along the train tracks that detect high temperatures in wheel bearings as the train passes. These are extremely limited and can detect bearings only in Stage 4 failure where catastrophic failure (a wheel burn-off) is imminent. An alarm requires immediate emergency action, disrupts train schedules, and is extremely costly.
2- Studying temperature ranges:
A newly patented technique is being evaluated that could have a significant benefit to industries that need to analyze bearing and lubrication life in difficult-to-reach areas, such as under train cars. This technique cancels all thermal surrounding variables except the increase in bearing temperature due to wear or lubrication failure.
Any recorded temperature variation would be a result of unwanted maintenance- or repair-related conditions such as over- or under lubrication, bearing damage, or misalignment. If one bearing is more than 15°C greater than another on the same shaft, the bearing health is in question and the cause of the increased bearing temperature must be determined. The bearing comparison is accomplished with electronic temperature sensors and comparators powered by a self-contained power supply that recharges its battery through the motion of the equipment.
The methodology involves the following:
• Temperature sensors are attached in close proximity to all the bearings on a common shaft or axle.
• The sensors apply input to a sensing unit that is self-contained and has wireless technology for communication with warning devices.
• The temperature data of each unit is analyzed and compared electronically.
• If any bearing temperature varies more than 15°C, an alarm is transmitted and an LED indicator will light.
• The system is self-powered by a small power supply which is actuated by the movement of the equipment.
• There is a maximum allowable temperature in case all bearings are out of normal operating range.
This technique will never be as accurate as oil or vibration analysis, but in remote or hazardous locations where these tools are not an option, it will provide an increased level of condition monitoring that was not available in the past.
#bearings #bearingfailure #bearingproblems #bearingdetection #بلي #فشل