Blog
- Super User
- General Knowledge
- Hits: 6064
Gearbox Maintenance
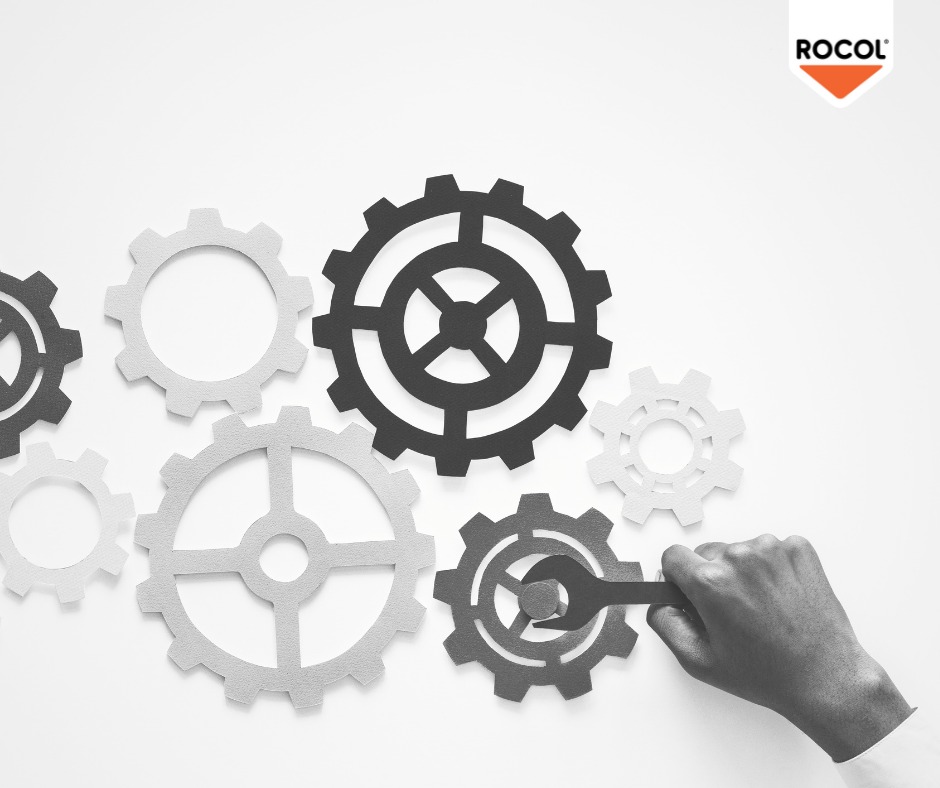
All gearboxes must receive periodic maintenance including an oil change. Oil should be checked regularly for contamination from dirt, debris, and other fluids such as water. The oil should also be changed periodically based on hours of operation and on oil temperature. Oil that operates at elevated temperatures (above 150° F) needs to be changed more often than oil that operates at 120° F. As the temperature increases up to 180° F, the oil change frequency increases significantly. Elevated temperatures accelerate the breakdown of the oil’s molecular structure thereby inhibiting its ability to form a protective film. If oil continuously operates above 200° F, a circulating lube oil system should be considered to cool the oil.
American Gear Manufacturers Association recommends that oil is supposed to be changed after the first 500 hours or 4 weeks of operation, whichever comes first. After the initial operation of the unit, AGMA recommends that oil is supposed to be changed every 2500 hours of operation or every 6 months, whichever comes first. AGMA further suggests that these intervals can be adjusted based on the gearbox system configuration as recommended by the manufacturer. Furthermore, having a condition monitoring program that identifies changes in the lubricant such as color, viscosity, oxidation, water concentration, contaminant concentration, percentage of sludge, and change in oil chemistry is important. There also a lot of additives that can be implemented to extend the lubricant change intervals.
In addition to oil, the physical condition of the gearbox including the foundation, protective coating, seals, breathers, circulating oil system, couplings, and bearings should be inspected periodically. A problem with any of these items identified in the early stage by plant personnel can help avoid a catastrophic premature failure of the gearbox. A worn bearing may cause wear on gear teeth, but prolonged operation in this condition can lead to more severe conditions resulting in broken gear teeth which can feed to other gears in the train and cause damage to more components that might not have otherwise required replacement. An adverse condition may not be obvious to the operator but a periodic inspection of the gearing and any changes or acceleration in wear patterns indicate that something has changed and it should be investigated.
Condition monitoring programs evaluate changes in operating parameters and provide valuable quantitative data that can help forecast when failures might occur. These services can be performed by in-house personnel or contracted. Oil temperature, level, and condition, vibration, noise and physical condition of seals and breathers are some of the parameters that should be monitored. After an initial baseline evaluation of the system, periodic inspections, photographs, and data analysis are used to identify and evaluate any changes or trends that might signal a problem.