Blog
- Super User
- General Knowledge
- Hits: 9358
5 Common Lubrication Problems and How to Fix Them
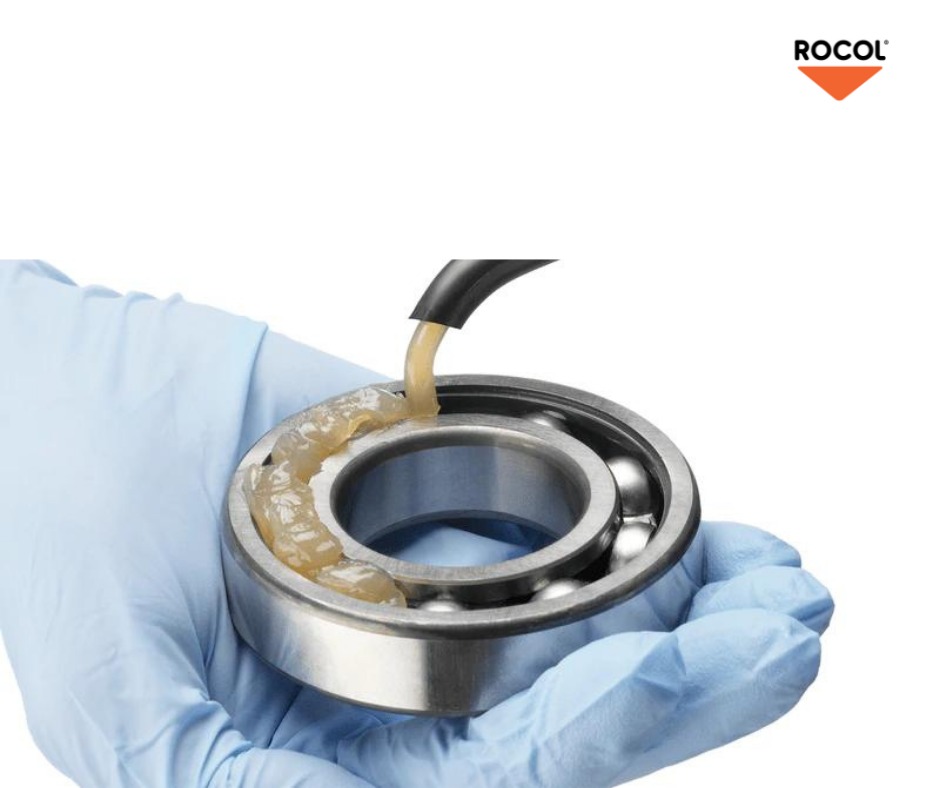
One of the greatest opportunities our technical engineers have is the chance to walk through various plants around the country. They visited power plants, food-processing plants, refineries, manufacturing facilities and a long list of others.
During these trips and audits, they have discovered several recurring lubrication issues that seem to be widespread throughout the industry. The following is a list of the most common problems and how they should be resolved.
1. Lack of Procedures:
Great lubrication programs are only as good as the people who do the work. However, the retirement of technicians has been the problem of greatest concern.
As a lot of people are reaching retirement age and subsequently retiring, they are taking with them a great deal of personal experience and knowledge of how they do their jobs.
Documented procedures can lessen the blow and help new personnel understand the proper way a task should be performed.
You want to write a procedure not only for the application of lubricants (oil changes, re-greasing, etc.) but also for how lubricants are handled in storage, decontaminated upon arrival and even disposed of after use.
Procedures should be developed with best practices in mind. For example, new oil should be sampled upon delivery to confirm its properties and tested for contaminants. If necessary, the new oil should be decontaminated before being released for service or put into bulk storage containers. In other words, you must design procedures in a manner that enables the lubrication program to reach a world-class level.
2. Improper Sampling Points and Hardware:
If used correctly, oil analysis can be an extremely valuable tool. It allows you to monitor not only the health of the oil but also the health of the machine, as well as catch failures before they become catastrophic. In order to obtain all the benefits of oil analysis, you first must have the correct sample points and hardware.
All machines to be included in the oil analysis program should be evaluated for the proper sampling hardware. Splash-bathed components such as bearings and gearboxes can be equipped with minimized sampling valves with pilot tube extensions.
Circulating systems should be examined for the best possible sampling points as well. These systems typically require several points.
3. Over greasing
Most plants I visit do not recognize that grease guns are precision instruments. They also fail to see the problems that can be caused by the misuse of grease guns.
Just like many other people, I was taught to grease a bearing by simply attaching the grease gun and working the lever until grease was seen purging from somewhere.
While this may be effective for hinge pins and other applications where purging grease won’t cause damage, it shouldn’t be employed for all grease applications.
Over greasing is a very common problem and can result in higher operating temperatures, premature bearing failure and an increased risk of contaminant ingression.
Bearings require a set volume of grease to be properly lubricated. A popular formula used to determine the volume of grease needed is the outside diameter (in inches) multiplied by the width (in inches) multiplied by 0.114.
This will provide the volume of grease in ounces that the bearing requires. Make your life easier and use our handy calculator for determining bearing grease volume and frequency.
Once you have calculated the volume of grease for the bearing, you need to know how much grease the grease gun is dispelling per stroke. To do this, simply pump 10 shots of grease onto a plate and weigh it on a digital scale. Next, divide the weight of the grease by 10.
This will give you the amount per stroke of output. Remember, certain grease guns can produce pressures up to 15,000 psi and can cause numerous problems if not properly managed.
While calculating the re grease requirements for all bearings onsite and determining the output of grease guns are a great place to start, there are other concerns that must be addressed as well. For instance, the output of grease can vary between guns.
The best way to counteract this problem is to standardize with a single type of grease gun so the output will be similar for each one. Grease guns should also be dedicated to a single type of grease and checked at least once a year.
4. Lack of a Labeling System:
Labeling is a key part of any world-class lube program. Not only does it reduce the chance for cross-contamination by minimizing confusion as to which lubricants go where, it also allows individuals who may not be as familiar with the lube program to top-up with the correct oil or grease.
Of course, labels can be used for more than just identifying lubricants. On a recent project, the lube labels were barcoded to allow all assets in the plant to be integrated into the computerized maintenance management system (CMMS) for automatic work-order generation.
The best label design incorporates a color/shape scheme for each lubricant used. This offers a quick visual reference as to which lubricant is inside the machine.
ROCOL has developed the Lubricant Identification System (LIS), which includes all basic information for a machine type such as base oil, application and viscosity. As mentioned previously, once a labeling system has been established, the labels should be applied to all lubricant storage containers and application devices.
5. Use of OEM Breathers and Dust Caps:
Most original equipment manufacturer (OEM) accessories like breathers do little to restrict the ingression of tiny particles into oil and critical spaces, which can damage machine surfaces. Some of these breathers are simply a cap filled with steel wool or a mesh screen that serves as a block for larger particles.
Considering the lubricant film in a journal bearing is approximately 5 to 10 microns, any particles of this size contaminating the oil will greatly increase the likelihood of wear and subsequent machine failure.
These tolerance-sized particles do the greatest damage and have the highest probability of causing machine wear.
Not only do many OEM breathers allow particles into the oil, they also do nothing to restrict moisture from entering the oil. Oil is hygroscopic, which means it absorbs moisture from the ambient air. In areas with high humidity or steam, moisture will pass through these types of breathers and be absorbed into the oil, causing rust, increased oxidation and hydrolysis rates, and a higher corrosive potential of acids formed by oxidation and hydrolysis.
OEM breathers should be replaced with higher quality versions to restrict particulate and moisture ingression. With several breather manufacturers on the market, the key is to get the breather that is right for your particular environment and operating conditions. In very dry environments, a spin-on particulate filter may work fine provided that ambient humidity is low. In more moist environments, a hybrid-style breather may be the best choice.
This type of breather employs a particulate filter to trap hard particles followed by a desiccating phase to strip moisture from the incoming air. All of these breathers can be threaded into the current breather port for quick and easy installation.