Blog
- Super User
- General Knowledge
- Hits: 2411
𝗪𝗛𝗔𝗧 𝗔𝗥𝗘 𝗔𝗘𝗥𝗢𝗦𝗣𝗔𝗖𝗘 𝗟𝗨𝗕𝗥𝗜𝗖𝗔𝗡𝗧𝗦?
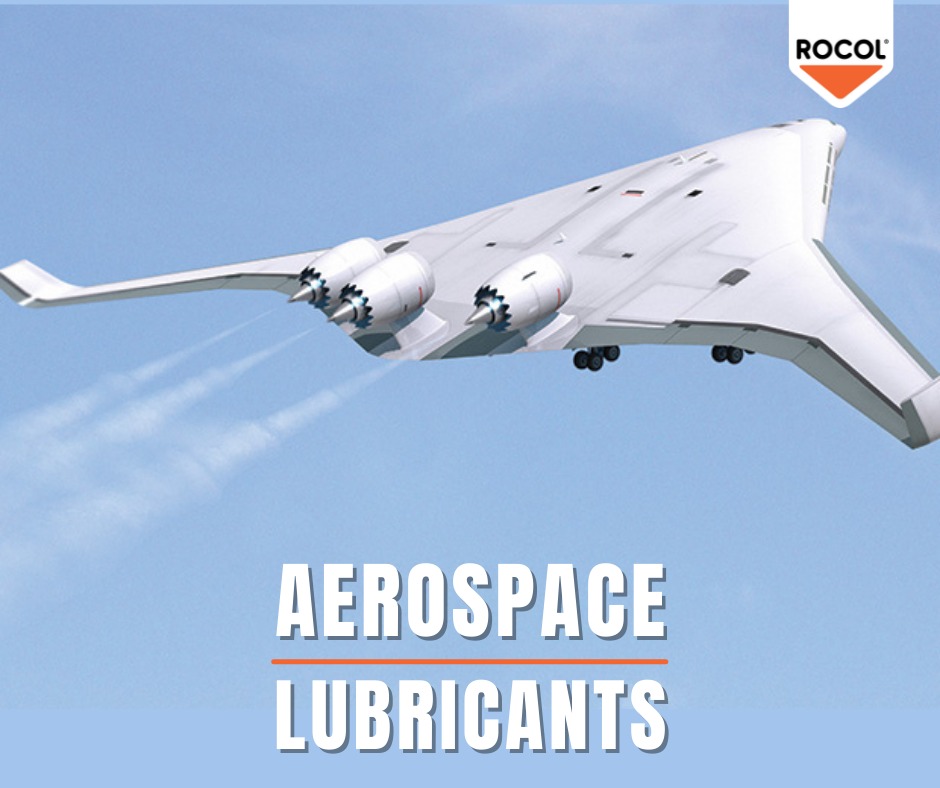
Selecting the most appropriate lubricant for aerospace mechanisms requires a selection of the most lightweight and most functional lubricant. This is because additional costs are incurred for every pound in total weight added during aerospace operations. Moreover, utilizing heavier lubrication would only cause significant financial consequences on top of possible mechanical or technical concerns.
Research on lubricants used in the aerospace industry would show that solid lubricants were traditionally used for aerospace machinery. However, the advent of technology, globalization, and modernization has brought about significant innovations in the field. New formulations of lubricants with the same, or even higher, quality performance have been developed and are now being utilized widely in many aerospace applications.
What are Aerospace Lubricants?
Lubricants that are used in aerospace applications such as, space travel, commercial airlines, and defense, are like other lubricants, but face more critical performance demands. In order to be classified as an aerospace lubricant, products must pass tests that are created by the Department of Defense (DoD) known as “MILSPECS.” To ensure safety and performance for aerospace applications, the MILSPECS create standardization to meet DoD objectives. These MILSPECS test different performance factors such as: corrosion protection, shear stability, compatibility, and water sensitivity.
What Differentiates Aerospace Lubricants?
In addition to meeting various MILSPECS, aerospace lubricants are engineered specifically for aircraft engines and fuel systems. The key difference between aerospace lubricants and non-aerospace lubricants like it has been mentioned before, is weight. In space operations, weight is crucial because more fuel is needed, which can become costly. It could also put a strain on how many other supplies could be included in the launch. As the safety of astronauts and functionality of equipment are vital, these lubricants cannot fail.
In aerospace applications, lubricants face the most demanding tests. With temperatures in space at near Absolute-Zero and reentry temperatures reaching 5000 F, lubricants must perform in a wider-range of temperatures than their Earth-bound equivalents. Additionally, lubricants must be able to operate in a vacuum environment. This is on top of all of the crucial navigational and life-supporting machines that make space travel possibly. These machines cannot suffer any breakdowns or down time as they support life and other functions both in space and on Earth. Aerospace lubricants must have a long life to maintain these critical operations.
In defense operations, completing the objective is key and your lubricant must perform to ensure the objective is met. These lubricants have to: withstand extreme-temperature jet engines, cargo aircraft landing gears, precise navigational tools, and other wide-temperature components. By selecting lubricants that meet the right MILSPECS, you can ensure proper performance and success in your aerospace operations.
Considerations in Selecting Aerospace Lubricants
In order to select the most appropriate lubricant, companies would usually conduct field tests using a variety of lubricants that are available in the market. Lubricants are evaluated based on their viscosity grade, machine operating contexts, volatility, sump cleanliness control, and rate of long-term use. Apart from this, companies would also determine compositional differences among available lubricants in order to determine their individual implications in costing and other operational concerns.
Studies have also found a general selection criterion for aerospace lubricants, as presented below. On top of the previously presented evaluative aspects, the following are the major considerations in selecting the most appropriate lubricant or solution in operations:
-Operating environment
-Fluid-film lubrication and viscosity
-Boundary lubrication performance
-Compatibility
-Fire resistance
-Stability
-Toxicity and biodegradability
-Susceptibility to additives
Aerospace Lubricants that are Available in the Market
Presented in the following sections are an overview of the lubricants commonly used in the aerospace industry.
Perfluoropolyether Lubricants (PFPEs)
The perfluoropolyether lubricant line saw its beginnings in the commercial market in 1965 when it was marketed as a lubricant with low thermal stability and low vapor pressures at low molecular weights. Composed mainly of oxygen, carbon, and fluorine, PFPEs are the least preferred lubrication solution in civil and military aerospace applications due to their complexity and relatively expensive costs. Apart from this, PFPEs are solid lubricants, implying possible weight issues during operations.
Most perfluoropolyether lubricants in the market utilize monomers acquired from crude oil, suggesting a labor-intensive process of developing even its raw materials. Companies that primarily produce PFPEs invest millions, or even billions, in capital in order to meet the necessary regulatory and operational standards required from perfluoropolyether lubricants to function appropriately in aerospace applications. Companies, however, are developing variations in PFPE components in order to make the product more marketable and less complex. For example, a prominent company that markets PFPEs utilize hydrofluoric acid from calcium fluoride to produce new monomers.
Generally, perfluoropolyether lubricants could be used in the following applications:
Rocket engines and support systems in ground operations
Engine oil and gearbox
Couplings (e.g. engine, oxygen system)
Bearings, ballscrews, and leadscrews
Aerospace instruments, gimbals, and gyroscopes
Research on PFPEs has shown that the material has a poor boundary that would be unable to solubilize newly-formulated additives. In addition, the lubricant was also found to be prone to autocatalytic degradation. These reasons further render PFPEs as an unpopular choice in addressing aerospace industry solutions.
Multiply Alkylated Cyclopentane (MACs) Lubricants
These lubricants have replaced traditional mineral oil-based lubricants due to their low volatile properties and superior candidate additives that are comparable with the performance of lead naphthenate additives and phosphate additives that are currently being utilized in aerospace applications. Moreover, a number of researches suggest that MACs yield better outcomes than PFPEs in room temperature conditions in vacuum environments. This suggests better application outcomes for MACs lubricants. General functions of multiply alkylated cyclopentane lubricants also encompass that of PFPE applications.
Current researches on MACs lubricants and other liquid-based lubricants are examining the use of more exotic products, such as ionic liquid lubricants, in furthering the capability of lubricants in addressing aerospace concerns.